- Ensure Patient Safety by addressing potential product risks before they cause harm
- Meet Regulatory Requirements by following established processes for complaint management, HIPAA compliant reporting, and audits
- Reduce Business Risk through proactive compliance measures that prevent costly enforcement actions, legal disputes, and market disruptions
Compliance with FDA Complaint Handling Regulations is essential for medical device manufacturers. The Medical Device Reporting (MDR) and Quality System Regulation (QSR) standards require manufacturers to implement processes that ensure accurate identification, documentation, and resolution of product complaints. These processes help maintain product safety, ensure continued market access, and reduce regulatory risks.
By following these regulations, manufacturers can avoid serious consequences, including FDA enforcement actions like Form 483 Observations, Warning Letters, and even Product Recalls. Effective complaint management also supports uninterrupted market access and fosters trust among healthcare providers, patients, and regulatory authorities.
This guide explains key FDA complaint handling requirements, highlights industry best practices, and demonstrates how MaestroQA can help meet regulatory standards while improving operational efficiency.
Why FDA Complaint Handling Matters
The FDA’s complaint handling regulations are designed to protect patients by ensuring that medical device manufacturers identify, investigate, and resolve product issues quickly and effectively. These regulations promote accountability by requiring manufacturers to document complaints, track recurring issues, and take corrective action when necessary.
Adhering to these standards helps manufacturers:
How MaestroQA Supports Compliance
MaestroQA empowers medical device manufacturers to meet FDA complaint handling requirements by:
- Ensuring Accurate Complaint Identification and Escalation: Detect reportable events early and ensure timely escalation following FDA protocols.
- Tracking Documentation Compliance: Maintain complete and consistent records of customer complaints, including device identifiers, issue details, and resolution steps.
- Generating Inspection-Ready Reports: Create audit-ready summaries with evaluation histories and compliance performance tracking.
- Automating Complaint Monitoring: Use AI-powered tools to monitor 100% of customer interactions and flag potential compliance risks for further review.
Understanding FDA Complaint Handling
The FDA defines a complaint as any written, electronic, or oral communication alleging a deficiency in a medical device’s identity, quality, durability, reliability, safety, effectiveness, or performance after distribution. To ensure product safety and regulatory compliance, manufacturers must implement formal complaint handling procedures as required by Medical Device Reporting (MDR) and Quality System Regulation (QSR).
These regulations cover the entire complaint lifecycle, from identification and evaluation to corrective action and record maintenance. This section breaks down the key FDA requirements and how manufacturers can meet these obligations.
Core Complaint Handling Requirements
Medical device manufacturers must establish clear, documented procedures for processing, evaluating, and investigating complaints. These procedures help ensure uniform complaint handling while meeting the FDA’s strict regulatory standards.
Uniform and Timely Complaint Processing
Medical device manufacturers must establish clear, documented procedures for processing, evaluating, and investigating complaints. These procedures help ensure uniform complaint handling while meeting the FDA’s strict regulatory standards.
Complaint Evaluation and Investigation
Every complaint must be evaluated to determine whether it qualifies for FDA reporting under MDR. If an investigation is warranted, manufacturers must document the investigation’s findings, conclusions, and corrective actions.
Required Data Fields and Documentation Standards
Manufacturers must document key complaint details, including:
- Device name, model, and unique identifiers (e.g., lot or serial number)
- Date the complaint was received
- Complainant’s contact information
- Nature and details of the reported issue
- Investigation results, conclusions, and corrective actions taken
- Response to the complainant (if provided)
Timeframes for Complaint Resolution
Manufacturers must define complaint processing timelines based on risk levels and potential impacts on patient safety. Delays in processing must be documented and justified.
Beyond Complaint Handling – Customer Interactions
The FDA’s QSR framework extends beyond complaints to cover broader customer interactions related to device performance. These additional record keeping requirements ensure that all customer communications are logged and evaluated for potential quality concerns.
Manufacturers must document the following customer support interactions, even when they don’t qualify as formal complaints:
- Technical Support Inquiries: Including troubleshooting steps and issue resolutions
- Training Provided to Customers: Including device use and safety precautions
- Routine Maintenance Communications: Including repair, replacement, or servicing records
- User Feedback on Device Operation: Including feature requests, product improvement suggestions, and usability concerns
By monitoring all relevant interactions—not just formal complaints—manufacturers gain visibility into how their devices perform in real-world use, helping them identify and address potential quality issues before they become safety risks.
How MaestroQA Supports FDA Complaint Compliance
Compliance with FDA Complaint Handling Regulations can be complex, but with the right tools, it becomes manageable. MaestroQA empowers medical device manufacturers by embedding quality assurance into complaint-handling workflows, transforming regulatory challenges into operational success.
Our platform simplifies compliance through automated monitoring, actionable insights, and tailored, HIPAA compliant reporting — ensuring every interaction meets strict Medical Device Reporting and Quality System Regulation standards.
By integrating MaestroQA into complaint-handling processes, manufacturers stay compliant while improving operational efficiency, reducing manual workloads, and enhancing overall product safety. Every interaction is monitored, every complaint is documented, and every regulatory standard is met with confidence.
QA Framework for FDA Complaint Handling
To meet FDA complaint-handling standards, manufacturers need a structured QA framework that ensures accurate complaint identification, thorough investigations, and compliance with Medical Device Reporting and Quality System Regulation standards. MaestroQA supports these efforts with custom scorecards, automated monitoring, and audit-ready reports.
How it Works
Core Evaluations: Ensure accurate complaint classification, timely resolution, and professional communication with customers.
Custom Scorecards: Use tailored scorecards to evaluate agent performance in handling complaints, conducting investigations, and documenting required data points.
Data-Driven Monitoring: Track metrics like complaint identification accuracy, investigation completeness, and customer service standards through live dashboards.
Audit-Ready Reporting: Generate inspection-ready reports with trend analysis, performance summaries, and full audit trails.
Key Sections from Tailored Scorecards
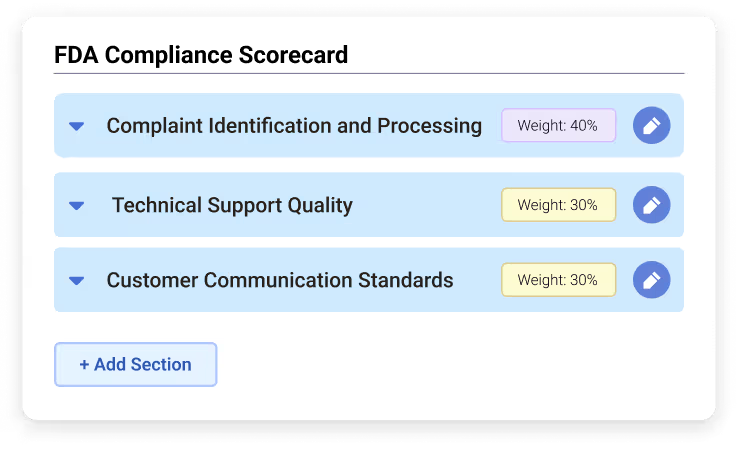
Complaint Identification and Processing: Evaluate agents’ ability to distinguish complaints from general inquiries, capture essential complaint details, and escalate reportable events correctly.
Technical Support Quality: Assess how well agents follow troubleshooting procedures, document interactions, and resolve technical issues according to established protocols.
Customer Communication Standards: Ensure agents provide clear, professional, and empathetic communication while setting accurate next steps and maintaining complete interaction records.
To see the full scorecard example and more details on the QA framework, explore the full QA Framework and Scorecard for FDA Complaint Handling to see how MaestroQA supports every stage of the compliance process.
Takeaway: Drive FDA Compliance with MaestroQA
Staying compliant with FDA complaint handling regulations doesn’t have to be complicated. MaestroQA empowers manufacturers to meet MDR and QSR requirements by automating complaint tracking, standardizing documentation, and ensuring audit readiness.
With MaestroQA, manufacturers can:
- Ensure Complete Complaint Documentation: Capture every detail required by the FDA, including device IDs, customer information, and investigation outcomes.
- Monitor Interactions at Scale: Review 100% of interactions with AI-powered tools that detect compliance risks and flag reportable events.
- Streamline Compliance Audits: Generate inspection-ready reports with complete evaluation histories and compliance performance summaries.
- Proactively Mitigate Risks: Uncover product trends, investigate root causes, and implement corrective actions before issues escalate.
Real-World Example: How a Leading Medical Device Manufacturer Ensured FDA Complaint Handling Compliance
A leading medical device manufacturer producing life-critical products needed to comply with FDA Quality System Regulation and Medical Device Reporting. To ensure ongoing compliance, they implemented a robust complaint-handling process that enabled precise documentation, efficient investigations, and continuous readiness for FDA inspections.
The company faced several compliance challenges, including:
- Accurate Complaint Identification: Customer service agents needed to distinguish complaints from general inquiries to ensure accurate classification and documentation.
- Ensuring Investigation Accuracy: Properly documenting complaints and conducting root cause investigations often required manual processes, increasing the risk of delays.
- Staying Inspection-Ready: They needed a reliable way to track investigations, create compliance reports, and prepare for unplanned FDA audits.
With MaestroQA, the company developed a comprehensive complaint-handling framework tailored to meet stringent FDA compliance standards. This included:
1. Comprehensive Complaint Processing System
- Multi-Channel Intake: The company captured complaints from phone calls, emails, social media, and healthcare provider submissions.
- Clear Complaint Identification: Customer service representatives were trained to distinguish product complaints from general inquiries and ensure complaints were classified and documented accurately.
2. Detailed Documentation Procedures
For every complaint, agents consistently logged:
- Customer contact details
- Device identifiers (model, lot, or serial numbers)
- A clear description of the reported issue
- The date the complaint was received
- Initial assessments and any immediate actions taken
3. Systematic Investigations and Escalations
- Root Cause Analysis: The company’s team conducted detailed investigations, evaluating reported issues for underlying causes and checking for recurring product failures.
- Corrective Actions: When safety issues were identified, corrective measures such as product recalls or updates were implemented.
- Safety Escalations: Safety-critical issues were escalated immediately, ensuring timely responses to potential hazards.
4. Continuous Customer Interaction Monitoring
In addition to complaints, the company tracked:
- Technical Support Requests: Documenting troubleshooting steps and customer service responses
- Device Maintenance and Training: Logging training sessions, maintenance requests, and user feedback on device performance
By implementing this structured process with MaestroQA, the company achieved:
- Regulatory Compliance: Required complaint details were consistently documented, ensuring compliance with FDA regulations.
- Reduced Compliance Risks: Safety-related complaints were identified and escalated promptly, reducing potential enforcement actions like Warning Letters or mandatory recalls.
- Operational Efficiency: Faster, more accurate investigations minimized service disruptions and product recalls.
- Inspection Readiness: Detailed, audit-ready records kept the company prepared for FDA inspections at all times.
By adopting a structured, compliance-driven approach, the company maintained full FDA regulatory compliance, minimized operational risks, and ensured continuous readiness for inspections. Their proactive complaint-handling process set a standard for managing safety-critical devices effectively while building trust with regulatory bodies and customers alike.
Conclusion
Navigating FDA complaint-handling regulations doesn’t have to be overwhelming. With MaestroQA’s structured QA framework, custom scorecards, and automated compliance tools, medical device manufacturers can simplify regulatory adherence while boosting operational efficiency. By embedding QA into daily processes, your team can ensure complaint accuracy, maintain complete records, and stay audit-ready.
Take the Next Step
Discover how MaestroQA can support your FDA complaint-handling processes with powerful QA tools, tailored scorecards, and audit-ready reporting. Contact us to learn more!
Legal Disclaimer: The information provided on this webpage is for informational purposes only and does not constitute legal advice. For specific advice regarding compliance with CCA or CDA regulations, please consult a qualified attorney.